In today’s world, technology has seamlessly integrated into various industries, with manufacturing being no exception. The journey towards total digitization is not a distant future – it is unfolding at present, transforming businesses of all scales. As organizations undertake this transformative journey, the emphasis transitions from mere technology investment to optimizing and profiting from these digital advancements.
In recent times, the global manufacturing sector has witnessed a radical transformation. The spur for this shift stemmed from the challenges presented by the pandemic, compelling the fundamental infrastructure of global commerce to grapple with unexpected disruptions in supply chains. Amidst these formidable trials, technology became more than a mere tool; it evolved into a lifeline, providing resilience and adaptability amid adversity.
We are at the onset of a new era in digital manufacturing. Manufacturers are embracing this transition, harnessing data-driven insights to propel themselves toward manufacturing practices that are both sustainable and efficient. A noteworthy example is highlighted in a study conducted by Workday, indicating that automation has the potential to reduce planning and reporting cycles in manufacturing by an impressive 50%-70%.
To seize the opportunities and embrace smart manufacturing, manufacturers must formulate a clearly defined IT strategy, thus enabling a heightened level of resilience. The year 2023 stands out as transformative, marked by the widespread and accelerated adoption of technologies such as AI, data analytics, cloud computing, edge computing and others. These technologies facilitate automation "at the source," consequently elevating efficiency with reduced reliance on centralized servers.
Digital manufacturing trends for 2024
Digital manufacturing trends for 2024 highlight three crucial pillars: Connectivity, Intelligent Automation, and Scalable Data Management & Analytics. Within these domains, a spectrum of technologies is poised to reshape manufacturing, including IoT devices, advanced analytics, AI-driven automation, and scalable cloud infrastructures.
Within these domains, a diverse array of technologies is positioned to reshape manufacturing. This spectrum includes IoT devices providing real-time monitoring, advanced analytics predicting maintenance needs, AI-driven automation optimizing production processes and scalable cloud infrastructures supporting the growing demands for data.
For manufacturers to succeed in the face of swift industrial evolution, it is imperative not only to observe these trends but also to proactively integrate them into their operations. We invite you to engage in the conversation and explore the technologies poised to define the future landscape of manufacturing excellence.
Trend #1: Smart factories reshaping shop floors
"Smart" factories represent a significant shift in manufacturing, introducing highly advanced and automated facilities that revolutionize conventional operations. Key technologies such as the industrial internet of things (IIoT), artificial intelligence (AI), automation, and digital twins play pivotal roles in this transformation. Projections suggest that the global smart factory market is on track to reach around $321.98 billion by 2032, exhibiting a CAGR of 9.52% from 2023 to 2032.
Smart factories elevate efficiency and enhance production processes through the integration of interconnected devices, smart sensors and real-time analytics. These innovations have found applications across a spectrum of industries, encompassing energy, power, automotive, oil and gas, electronics, and semiconductors. For example, the Tesla Gigafactory in Germany integrates solar panels as part of its commitment to sustainability, thereby reducing operating costs. Similarly, BJC Healthcare in the US has embraced smart manufacturing, incorporating IoT into its processes. The company leverages Radio Frequency Identification (RFID) technology to track medical supplies, resulting in reduced costs, heightened operational efficiency, and an overall enhancement of the company's functionality.
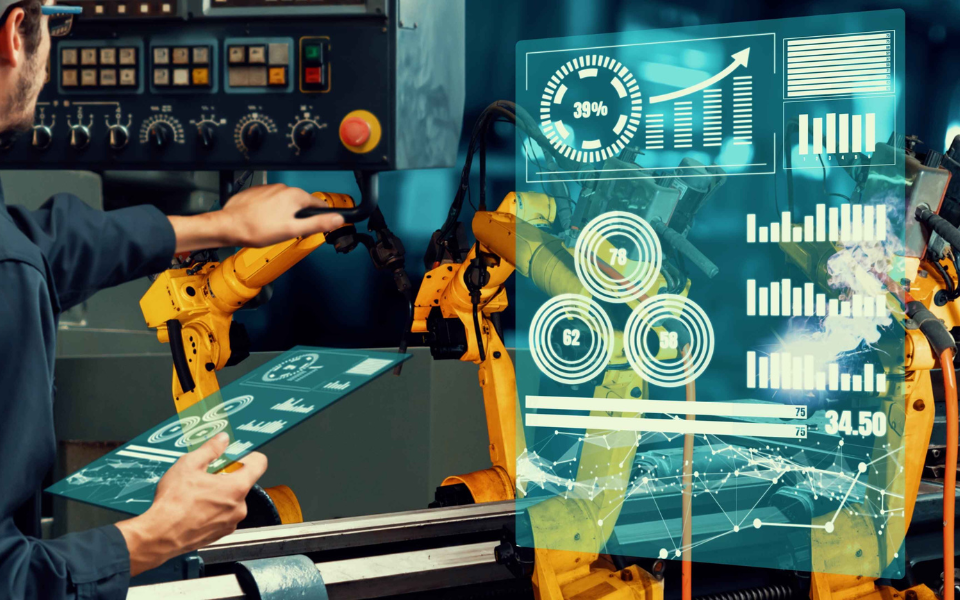
Emergence of Digital Twin Technology
The advancement of cutting-edge technologies is driving the ascent of digital twin technology in manufacturing, establishing a digital replica of physical processes to facilitate informed decision-making. A noteworthy illustration is Ford's implementation of AI-driven predictive maintenance through digital twin technology. Ford develops distinct digital twins for each vehicle model, encompassing various production stages from conception to operation. These digital models extend to manufacturing procedures, production facilities and the overall customer experience. Ford's digital twin precisely identifies energy losses, identifies areas for energy conservation, and enhances the overall performance of the production line. The increasing popularity of digital twins is evident in projections, foreseeing a market size of $73.5 billion by 2027.
Crucial role of AI/ML in manufacturing
The strategic utilization of AI provides manufacturers with the capability to methodically analyze extensive datasets, recognize patterns and enable informed decision-making. Within supply chain domain, AI plays a vital role in predictive analytics, enhancing inventory management, fine-tuning demand forecasting and streamlining logistics. This is exemplified in enterprises like Amazon, where AI-powered algorithms are employed to accelerate deliveries, effectively bridging the gap between their products and customers.
The impact of AI extends far beyond the supply chain, as explained by Haier Group, a prominent consumer electronics and home appliances manufacturer in China. The group has seamlessly incorporated AI into its manufacturing processes within the framework of a smart factory. This integration elevates various facets, including quality detection, machine collaboration, material transportation, maintenance, security and energy management. The Haier Group's case highlights the diverse applications of AI in contemporary manufacturing, illustrating its potential for enhancing operations and efficiency across a spectrum of industries. The trajectory of AI suggests that Generative AI will assume a central role in the forthcoming years.
Significantly, discussions surrounding AI would be incomplete without acknowledging machine learning, a pivotal component in predictive analytics for quality control. Machine learning algorithms play a substantial role in proactive measures aimed at improving product quality and optimizing manufacturing processes. Notably, a significant two-thirds of manufacturing companies attribute substantial revenue savings or generation to advanced analytics and machine learning.
A Remarkable Paradigm Shift
Furthermore, technologies such as augmented reality (AR) and virtual reality (VR) introduce an immersive dimension to manufacturing. They empower users to enhance their senses with real-time data from any location, ensuring constant and accurate awareness of the factory's status at all times. Additionally, the evolution of Web 3.0 amplifies machine interactivity through advanced technologies like AI, deep learning, ML, Big Data and data analysis. This enables machines to comprehend information in a manner similar to humans, employing language comprehension technologies and leveraging the Semantic Web.
In the manufacturing domain, a distinctive paradigm shift is unfolding with the advent of Collaborative Robots (Cobots). These human-powered robots operate alongside humans, contributing to efficiency by providing strength, power, precision, and valuable data. Importantly, the integration of AI technology facilitates their ease of programming and rapid learning, representing a significant leap forward in the manufacturing landscape.
Trend #2: Tackling supply chain challenges with blockchain
Blockchain technology emerges as a truly transformative tool in addressing challenges within the digital manufacturing supply chain, particularly in enhancing transparency and security. By establishing a tamper-proof record of transactions, the integration of blockchain in the supply chain empowers manufacturers to meticulously trace products throughout their entire lifecycle, from raw materials to finished goods. This resilient and unalterable ledger system stands as a guarantee for authenticity and data integrity.
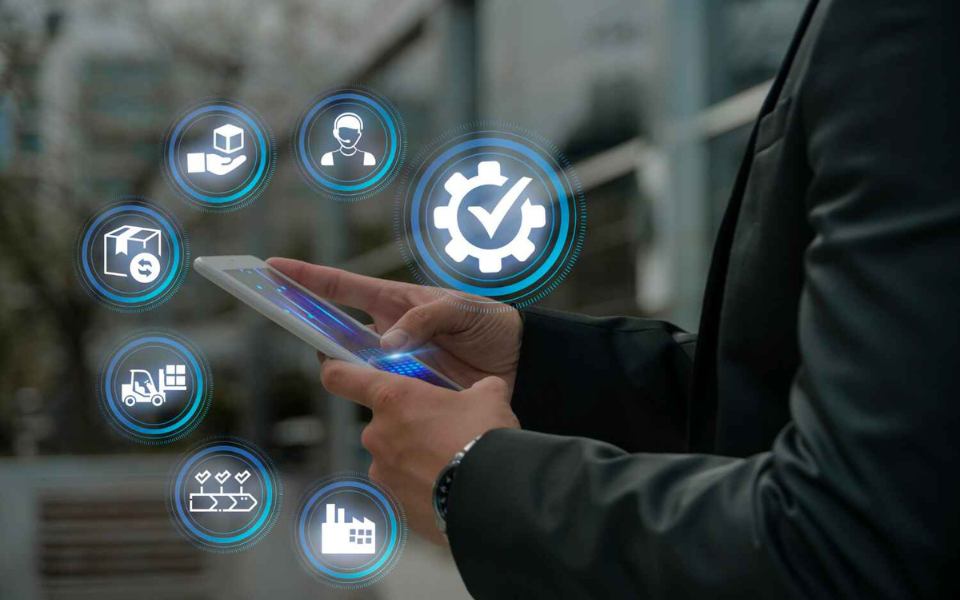
Blockchain technology also provides manufacturers with the opportunity to optimize operations, achieve enhanced visibility in supply chains, and precisely track assets, as indicated by insights from PwC. An illustrative example is Walmart, a retail giant, strategically employing blockchain technology to oversee their leafy greens suppliers. The objective is to ensure product safety and expedite the process of providing evidence in case of a claim. The system meticulously gathers data at each stage of the greens' journey, starting from the planting of seeds. Even after the greens reach the shelves, Walmart continues to contribute data to the platform, showcasing a commitment to transparency and accountability in their supply chain.
Currently, 24% of industrial manufacturing CEOs are either in the exploration phase or actively implementing this transformative technology. As the significance of cybersecurity and data privacy intensifies, directly influenced by the ongoing digital transformation, the prevalence of Blockchain applications in the manufacturing industry is anticipated to rise shortly.
In the coming 2–10 years, several futuristic technologies are poised to exert significant influence on the future of manufacturing. These include intelligent process automation, Cobots, autonomous mobile robots, AR/VR/MR/metaverse, Web 3.0 and knowledge engineering, neuromorphic computing, intelligent edge, quantum computing, 4D printing, 6G and c-band, zero trust security, resilient and self-healing systems, self-diagnosis systems and fully homomorphic encryption.
Navigating the hurdles of digital manufacturing
Embracing digital transformation introduces a set of challenges for manufacturers. Modernizing legacy systems, for instance, entails substantial investments, encompassing hardware upgrades and the standardization of data formats. The efficient management of diverse data sources demands robust strategies and advanced analytics. Cybersecurity emerges as a crucial concern, calling for multi-layered defenses and compliance with privacy regulations. Finally, tackling the skills gap and overcoming resistance to change in the workforce necessitates targeted training programs, clear communication, and stakeholder engagement to ensure successful digital adoption.
Endless opportunities
The manufacturing industry stands on the brink of a remarkable transformation in 2024, where the dynamic challenges of business meet the convergence of cutting-edge technologies. This amalgamation is set to revolutionize efficiency and ignite innovation in unprecedented ways. Additionally, supply chain complexities will transcend being mere obstacles; they will serve as pivotal catalysts for change, fundamentally shaping the future of manufacturing.
For manufacturers, comprehending these shifts is of utmost importance. These changes are not just minor adjustments to existing processes; they signify a paradigm shift, marking the dawn of a new era in manufacturing execution and strategy. It goes beyond mere adaptation; it involves a complete reimagining of the manufacturing ethos for 2024 and beyond.