The circular economy aims to increase reuse and reduce waste in manufactured products. However, product lifecycle management is typically limited to new product introduction, rather than considering end of life re-use. Circularity is an opportunity to close this loop, for a lower environmental impact, and better business outcomes such as an improvement in gross margins from material cost savings.
The circular economy
The deserts of Mojave in California are the resting place for aircraft at the end of their life, with unclaimed material lying around. The shipyards along the beaches of Alang in Gujarat, India carry out the bulk of global ship-breaking activity polluting the atmosphere with their asbestos byproducts. The Great Pacific garbage patch is an accumulation of plastic used by humans, with 1 to 2 million tons entering the ocean from rivers every year. Such waste can be avoided by adopting a circular economy to save the environment, while creating sustainable and profitable business models.
The Ellen MacArthur Foundation was established in 2010 as a thought leader for the circular economy, to influence decision makers across business, government and academia. According to the foundation, the circular economy is a new way to design, make and use products by designing out waste and pollution and regenerating natural systems (Figure 1).
The foundation has estimated savings due to circularity from material costs alone upto $ 700 billion annually for the global fast-moving consumer goods sector as an example.1 As much as 20 percent savings in material costs can be achieved in this industry, directly improving the gross margin, according to the report. Specific instances for circularity are biogas generation from household food waste and cascading the spent grains in breweries as livestock feed. And it is not limited to recycling of materials at the product’s end of life. It is a holistic perspective enforcing product makers to keep it in mind at all stages of the product lifecycle and not as an afterthought.
For equipment makers, the traditional focus of product design has been on ‘design for manufacturability’. Its objective is to quickly introduce a new product, adhering to quality standards at the lowest cost possible, and not to worry about what happens to it at the end of its life. But ‘design for circularity’ should include proactive planning and management of the entire life of parts from their design to their making, service and end of life, with maximum reuse.
To plan for circularity, the four building blocks of a circular economy as defined by the foundation are:
- Circular product design and production from the early design stages, specifying the purpose and performance of end-products
- New business models that have performance-based payment, not ownership of products
- Reverse cycle including supply chains to create value from materials and products after their usage
- Enablers and favorable conditions for an ecosystem - education, financing, collaborative platforms
The circular approach is as much a cost-saver and a sustainable business model as it is a positive impact on the environment. Apple, for example, uses Daisy the robot to disassemble 15 iPhone models at the rate of 200 phones per hour to retrieve valuable materials, according to its press release.3 Cobalt, a key battery material is recovered and sent up the value chain for reuse. Key components are made from 100 percent recycled tin and aluminum. Automobile maker Mahindra in India has setup a joint venture called CERO along with the government. CERO is the country’s first authorized vehicle recycler for the organized shredding and reuse of metals from vehicles at the end of their life.
Figure 1. The circular economy — an industrial system that is restorative by design
Transforming PLM for a circular economy
In order to achieve the building blocks of a circular economy, there are two broad initiatives that equipment makers should adopt for product development in its evolution to match industry needs. Product lifecycle management (PLM) is the workflow platform on which these changes can be implemented.
- Become closed-loop in nature by consolidating valuable information and its flow from multiple stakeholders. The stakeholders include humans such as employees, customers, suppliers, partners, dealers, regulatory bodies as well as technologies such as the internet of things and social media for product performance feedback.
- Change the way products are designed, especially to include newly evolving business models such as servitization, through which the product will be taken to the market.
PLM has its origins in American Motors Corporation (AMC) in the 80’s as a tool to improve the productivity of its design engineers.4 Development of new products, specifically Jeeps, was sped up by the creation of one central database which enabled users to access part drawings, 3D models and documents and to decide on engineering changes. When Chrysler bought AMC and adopted this system widely, it reported product development costs that were half the industry average, according to Microsoft Dynamics4 and other sources.
But PLM cannot limit its scope to the cost reduction of product development if it is to support the shift to a circular economy. It must evolve beyond that.
Closed-loop PLM
The following are ways in which PLM can evolve to become closed-loop and act as the central repository of valuable product performance insights. Information flow should happen seamlessly across the enterprise and in both directions – from the originating product design to different functions and departments, such as manufacturing, logistics and field services to reach the end customer and then a reversal of the flow.
Sequential work flow with feedback
The most common way a PLM system works is through a sequential work flow across functions and departments (Figure 2). The challenge with this model is that waiting times can be lengthy at each step, with rework required often, and vital information lost at times. Governance is key at each stage to ensure that there is no compromise on quality. Feedback at each stage should be passed on to the previous stage without any loss of information, to take necessary corrective action before proceeding.
In fact, this linear approach can have catastrophic consequences if there is no feedback and governance gets out of hand. Individual teams can end up focusing on small parts of the engineering process, none having the big picture perspective or complete view of the new system. This can lead to product failures, and even dangerous outcomes. Indeed, this is the situation that the New York Times alleges occurred at Boeing in relation to the infamous MCAS system in the 737 MAX aircraft.5
Figure 2. A linear product lifecycle management approach
Concurrent engineering with real time collaboration
In order to overcome the challenges of the sequential flow approach, concurrent engineering became popular toward the end of the century. It is a collaborative approach that needs a cultural transformation among team members. It is cross-functional, bringing together engineering, manufacturing and other functions. Decisions can be taken collectively to avoid rework and delays. Tasks can be done in parallel.
PLM as a tool provides features for making product development concurrent and collaborative. It is web-based for transparent, anytime access to multiple stakeholders. It has communication tools for status updates. Visualization allows team members to see any part from multiple perspectives at the same time, even before it is physically created. Feedback can be passed on quickly from one team to another during early stages of design. If manufacturers integrate these features into the way product design is carried out, they can enable stronger real-time concurrent engineering.
For example, ABB flipped its compartmentalized way of working when it implemented an online product configurator.6 This enabled the business to take inputs on configuration preferences directly from clients when engineers were designing future products. This “co-creation” of products, with product managers, customers and other internal teams sharing design solutions, resulted in reduced product complexity and better customer outcomes. The cycle time for designing and delivering a product was also reduced significantly, from months to weeks.
Collaboration outside the enterprise with crowdsourcing
To extend the concept of concurrent working beyond the enterprise in the age of the ubiquitous internet, outside sources from anywhere in the world can be tapped. GE has been using Fuse as its platform for crowdsourcing since 2016. It is connected to a network of micro factories for rapid design and prototyping.
GE posts its customers’ pain points as challenges to be solved, on Fuse, with a description, timelines and rules. Participants get their questions answered and submit their response. The submissions are evaluated to select the winners. Winning entries are forwarded to the technical team for further development.
A jet engine bracket is an example of part redesign by GE using crowdsourcing. The requirement was to make it 30 percent lighter while maintaining its structural integrity. When it was announced as a competition, 700 options were received. The winning entry was 84 percent lighter and met stiffness requirements, according to GE’s press release. Lego uses its crowdsourcing platform called Ideas, to enable the public to submit their ideas as new designs for toys. Winners are decided based on votes received from community members. They receive 1 percent of the revenue from their design as royalties.
Serialization of vital parts
The circular economy is not just about recycling materials. Parts can be repaired and sent back to the field to be used again. Providing unique serial numbers to each physical instance of a part will help in tracing its life cycle including visits to repair shops. Hot gas path components in the aircraft and turbine industry is one such example where parts are serialized. These are high-cost parts, subjected to the harsh conditions of combustion, and are critical to the efficient and reliable functioning of the system. Serialization can be extended to vital parts in other industries where the material or the process used to create the part are valuable. Serializing parts of high value will help PLM track product performance at an individual part level.
At the cutting edge of this area is the Mobility Open Blockchain Initiative, a consortium founded by leading automobile producers in 2018 for vehicle identification standards and lifetime transaction documentation. Honeywell’s GoDirect Trade e-commerce platform uses a blockchain for trading aerospace parts. This reduces the number of counterfeit parts getting into the market. Parts that are recovered from end-of-life products are tagged and stored on the blockchain with a secure history of the part. Each change of ownership and milestone in its lifecycle will be stored with no risk of loss of any information.
Predictive digital PLM
The above approaches focus on the product’s design and its making. Emerging technologies such as the internet of things extend the frontiers of PLM beyond the factory to the customers’ premises. As a concept, digital PLM extends product development beyond just design to perform real-time simulations, what-if scenario analyses and experiments for new products, predominantly digital in nature. Feedback from such experiments in real-time from connected assets in the field can be leveraged to make any corrections.
An example is GE Energy’s digital replica of a power plant. It models the plant including critical components, considering fuel cost and the price of electricity. Plant operators can use the model to optimally manage the trade-offs in operation. According to GE, its customer was able to achieve a 2 to 3 percent additional MW hour output resulting in a $15 million savings per plant.7
Changing the way product design works to cater to new business models
Information is valuable when it enables a profitable business model with growth opportunity. It should support new ways of designing products and taking them to the market. The following suggestions transform the way new products are conceptualized, developed and managed during their productive life in the field and beyond.
Product effectiveness-based PLM
Organizations should measure the effectiveness of new product introductions for successfully bringing them to markets with a healthy profitability, market share and a plan for circularity.8 One of the reasons for the high rate of failure noticed among new product initiatives is the lack of a feedback loop to integrate multiple product functions. This should be corrected. The process begins with an estimation of the existing status using product effectiveness parameters. Maturity scores are allocated to each parameter based on responses from subject matter experts. A Product Effectiveness Index is calculated for diagnosis. .
Based on the diagnosis, a set of initiatives are devised for the organization to improve the score. Examples for initiatives are process harmonization, system engineering robustness, integrated requirement gathering, concurrent engineering, green compliance and design automation. As a tool, PLM can then be customized according to the initiatives.
Agile ways of working
Concurrent ways of working avoid multiple hand-offs between departments during product design. But the time for individual tasks and hence the overall cycle continues to be long. To address this issue, manufacturing borrowed the agile approach for product development from the software industry. Short cycles that typically last for a few weeks are used to define and implement small, clearly defined ideas and upgrades. Each cycle is called a “sprint”.
BMW follows an agile way of working called LeSS or Large Scale Scrum, for developing its autonomous cars.9 Scrums are a way of working in an agile fashion, repeatedly delivering working and tested software that adds value for the customer, progressing towards a goal with each iteration (Figure 3). Teams are reorganized based upon product features, with end-to-end responsibility. Team members produce significant results in two-week sprints. These results can be tested in actual vehicles.
Figure 3. Short sprints for frequent cycles of new product introductions and upgrades
Servitization during the productive lifecycle
Servitization can be a powerful business model to support circularity after a product is installed for use. It is a pay-per-use model with contractual obligations between the product maker and the customer. Remote monitoring of product performance ensures its uptime. Maintenance and repair can be planned proactively with no impact to customer operations.
According to a study conducted by Aston University and Xerox, servitization has the potential to represent upto 50 percent of a company’s revenues.10 Information about post-sale services will be vital in PLM in order to understand how well a product is performing and take any corrective measures in future design cycles. The internet of things and social media will be the streams of data inflow for mining valuable product performance insights.
The servitization business model also builds in the cost of refreshing and upgrading the product as it evolves. This becomes a natural incentive for the manufacturer to design its products in a way that make them easily reusable, recyclable, or upgradable – reducing waste and increasing profitability.
PLM and the United Nations’ Sustainable Development Goals
The adoption of a circular economy with PLM as the implementation platform has benefits beyond the enterprise to the broader society. The fundamental assumptions based on which an enterprise has been setup can change. Its benefits can be mapped to the Sustainable Development Goals adopted by the member nations in 2015 for protecting the planet, peace and prosperity by 2030. These are regulatory in nature with governments not necessarily tracking them. Organizations can be proactive in compliance by transforming their PLM cycle. The following are the SDGs that a circular economy can impact directly:
The benefits of the combination of a circular economy and PLM reach the society and not just enterprises
- SDG #9: Industry, Innovation and Infrastructure – The new business models that are a result of a circular economy promote innovation. They create employment opportunities and infrastructure when new factories, energy sources and supply chains are built.
- SDG #12: Responsible consumption and production – The material savings enabled by the circular economy by means of reuse, recycle, repair and refurbishment of products reduce the overall consumption and hence the production needs.
- SDG #12 – Climate action – Circular economies result in responsible organizations and individuals by reducing the carbon emission and footprint in several ways – usage of renewable energy sources, indirectly reducing fossil fuel usage and electrical traction instead of internal combustion engines.
- SDG #4 – Quality education – Circular economies are an opportunity to reskill not just the employees in an enterprise but the entire ecosystem for the new ways of working and technologies used. Reskilling is a key driver of today’s economy resulting in education and eventually employment.
PLM as a foundation for a circular economy
Closing the loop and changing design processes are crucial shifts that PLM needs to evolve to support so that it can move away from just being an operational, visibility and cost management tool to a framework for the overall lifecycle of products (Figure 4). Circular PLM is a step in the journey toward distributed digital fabrication, where customers evolve into creators using technologies such as additive manufacturing.
The circular economy has grabbed the attention of policy makers and political leaders as a green initiative for future generations. It is now the turn of business and technology leaders to transform product development to make this initiative not just green but a profitable and sustainable revenue stream.
Circular PLM is a critical step toward distributed digital fabrication allowing customers to evolve into creators
PLM will be a key enabler for digitized product development. It should transform itself as the central repository for the closed-loop, seamless flow of information related to product design. It should fundamentally change the way product design is carried out to cater to the needs of new business models in a circular economy.
Figure 4. A framework for PLM as the platform for a circular economy
References
- Towards the circular economy—opportunities for the consumer goods sector, Ellen MacArthur Foundation, https://www.ellenmacarthurfoundation.org/assets/downloads/publications/TCE_Report-2013.pdf
- From linear to circular: Accelerating a proven concept, World Economic Forum, http://reports.weforum.org/toward-the-circular-economy-accelerating-the-scale-up-across-global-supply-chains/from-linear-to-circular-accelerating-a-proven-concept/
- Apple expands global recycling programs, April 18, 2019, https://www.apple.com/in/newsroom/2019/04/apple-expands-global-recycling-programs/
- Leapaldt, Andy, Making PLM and ERP work together, https://community.dynamics.com/b/communityteam/posts/making-plm-and-erp-work-together
- Boeing built deadly assumptions into 737 Max, blind to a late design change, The New York Times, June 1 2019, https://www.nytimes.com/2019/06/01/business/boeing-737-max-crash.html
- ABB product configurator: a case study, Infosys Knowledge Institute, October 2019, https://www.infosys.com/about/knowledge-institute/insights/Documents/abb-product.pdf
- Digital twin creation, GE, https://www.ge.com/research/offering/digital-twin-creation
- Sudarshan, Donekal Radhakrishna Rao, Kavanaugh, Jeff, System and method for customizing product lifecycle management process to improve product effectiveness, United States Patent No. US8799044B2, Aug 5, 2014.
- BMW Senior VP talks about the Autonomous Driving Campus, https://www.bmwblog.com/2018/12/21/bmw-senior-vp-talks-about-the-autonomous-driving-campus/
- UK manufacturing must embrace services boom, May 22, 2013, https://news.xerox.co.uk/news/u-k-manufacturing-must-embrace-services-boom
Originally published at PLM and product design for a circular economy (infosys.com)
Click through to know more about Infosys Sustainability Practice
About the Authors
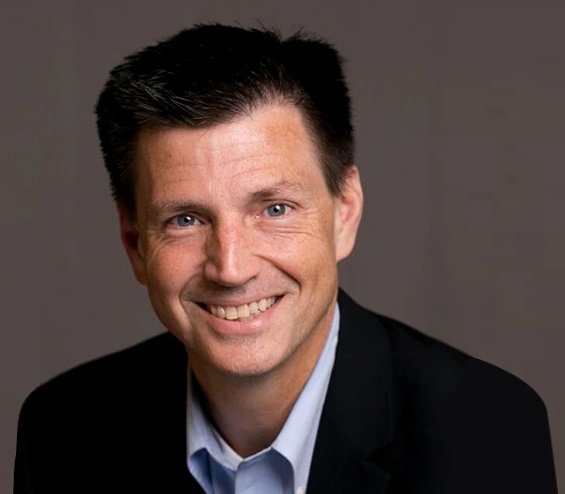
Jeff Kavanaugh - Vice President, Infosys Knowledge Institute
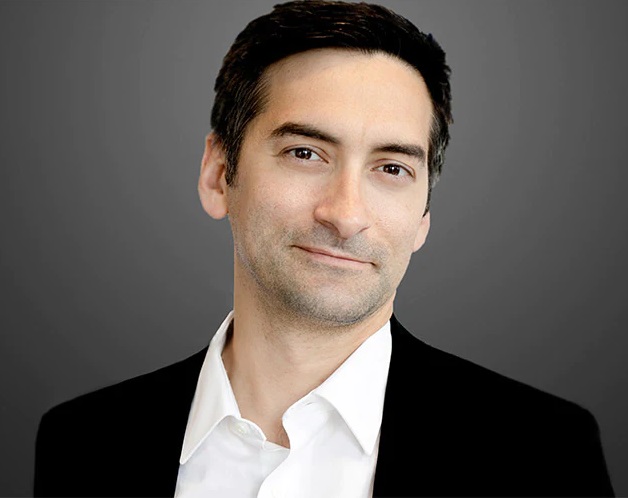
Samad Masood - Senior Principal, Infosys Knowledge Institute

S Ramachandran - Manufacturing and Engineering Lead, Infosys Knowledge Institute