Introduction
The manufacturing industry has witnessed its worst successive five months (February-June 2020)1, over the last seven years. The JP Morgan Global Composite Purchasing Managers’ Index (PMI) plummeted from an average of 52.47 points between 2013 to end of 2019 to a record low of 26.50 points in April of 2020, the lowest since the 2008-09 economic slump. However, after the initial wave, governments have announced a slew of stimuli to kickstart economic activity. Using that to their advantage and relying on their inherent resilience, manufacturing organizations have restored their manufacturing capabilities in a short period. As a confirmation, the PMI is on the rise since July.
Fig. 1 JP Morgan Global Composite PMI 2013-2020 Data1
The Covid-19 induced economic depression has reportedly led to an estimated 10 percent drop in income earned by workers globally in the first nine months of 2020, equivalent to a loss of over US$3.5 trillion.2 However, governments around the world have relaxed restrictions and provided stimuli for economic growth. In this paper, we look at the impact of supply chain disruptions on manufacturers and see how they can grow through the rapid adoption of digital solutions and display agility in adapting to new business contexts.
Unprecedented Global Situation – Factors Influencing Supply Chain Operations
The manufacturing industry had flourished over the last few decades, thanks to the widespread globalization of suppliers and customers. With the pandemic, almost 75% of companies reported supply chain disruptions across their ecosystem. The disruptions and operations lockdowns have led to over 80% of manufacturing firms resigned to the revenue decline in 2020.
Fig. 2: Challenges faced by manufacturing organizations during the Covid-19 pandemic
Sales and Operations Planning: Volatile demand globally caused by erratic purchases and a change in buying patterns have impacted the most sophisticated forecasting and planning algorithms. Health consciousness, the need to conserve funds and government policies prohibiting mass gatherings have led to changes in the way consumers buy. Moreover, job losses due to the economic downturn reduced purchases in cyclical industries such as automobiles, discretionary consumer goods and real estate. Health and savings assumed priority, and consumers spent less on seasonal purchases like fashion merchandise and cold desserts. A large global beverage manufacturer saw a steep decline in sales due to a lack of footfall in restaurants, resulting in a considerable drop in production.
Sourcing and Procurement: Low predictability of supply with regions moving into and out of lockdown multiple times and inconsistent rise in pandemic cases has led to long lead times, closed transportation routes and low supplier visibility for raw materials. This is especially true of supply from upstream manufacturing hubs such as those in South Asia or Southeast Asia, notably China and India. Switching to alternate suppliers resulted in delays, potential compromise of quality and significantly higher price of procurement. Many hi-tech manufacturers had to reduce capacity and service levels due to the shutdown of their primary component supplier, located in one of the regions worst affected by the virus.
Inventory Management, Warehousing and Logistics: Inaccurate demand forecast, unpredictable sourcing, lack of transportation or delivery options and irregular manufacturing schedules have led to either raw material stock-outs in some plants or surplus idle inventory or finished goods in others. Manufacturers are unable to preserve perishable goods (e.g., processed food, pharmaceutical drugs) due to the unavailability of appropriate storage options. There has also been a dip in the quality of non-perishable goods due to environmental exposure, e.g., rusting of iron bars. Such incidents have significantly impacted operations thanks to the increased cost of storage and low utilization percentage.
Production Planning and Manufacturing Operations: Production planning and manufacturing shift operations have become increasingly difficult with the absenteeism of skilled workers . Health concerns have forced people to stay indoors, leading to difficulty in adhering to shift plans and unavailability of trained personnel at designated machines. An aircraft MRO plant had to reduce production shifts due to uncertain demand, unavailability of human resources, and necessary resources. This saw aircraft layoffs and a reduced number of scheduled flights. Further, the efficiency of high-touch production lines with limited automation has suffered from the need to observe physical distances on the shop floor. Large manufacturing industrial carriers had to spread one shift’s workload to multiple shifts, to limit the number of people at a given time, incurring higher costs and delays in meeting customer demands.
Site Maintenance and Servicing: Safety concerns among MRO personnel and social distancing norms have impacted asset maintenance and field service leading to lower asset utilization due to unplanned machine outages.
Sales Pricing: Apart from reduced consumption, protectionist government policies and trade barriers like a ban on imports from lower-cost countries and imposition of higher duties have led to sharp price rise and lower sales.
Finance and Control: The limited cash in hand situation has affected consumption as well as payment to suppliers leading to longer payment terms and higher days’ sales outstanding (DSOs). This puts significant working capital pressure on organizations, with small scale manufacturers struggling to survive with low liquidity.
Human Resource Management: With few options for remote operations, many factories are saddled with the problem of a stranded and ailing workforce. Restrictions on travel and the inability to meet and drive business decisions onsite have hampered business growth.
Digitalization as the catalyst to drive growth – the way forward
A recent article in Forbes, The COVID-19 Problems That Will Force Manufacturing To Innovate, correctly said that the decision of “choosing not to respond quickly is choosing not to respond at all.” Now is the time for CXOs to necessarily invest in technology levers like artificial intelligence/machine learning (AI/ML), the Internet of Things (IoT), robotics, augmented reality/ virtual reality (AR/ VR), Big Data and blockchain, along with cloud or 5G adoption for product innovation and plant digitalization. Digital disruptions will provide organizations with the nimbleness to react faster during a crisis. It can help meet evolving customer needs and help shape the demand of customers with innovation while reducing dependence on the physical presence of factory workers. Adopting technology can open new business opportunities and introduce much needed business agility, resilience in business operations, efficiency gains and cost savings through remote operations, ecosystem integration, autonomy and alternative technology solutions.
Adoption of Digital Options
CXOs worry over the intensity of a digitization program, the speed with which digital transformation can de-risk production operations and deliver benefits.
The typical goals of a Chief of Production Operations are -
- Maximize worker safety - minimize safety incidents over time
- Increase throughput or capacity utilization - ensure higher productivity, flexibility and OEE
- Higher quality, lower defects - increase product quality by ensuring lower product replacement requests and quality rejects on the shop floor
- Reduce the cost of manufacturing - minimize idle time in process cells, increase capacity utilization and higher uptime, ensure quick resolution of any machine-specific issues
Fig. 3: Digital Solutions that positively impact KPIs of manufacturing organizations
Safe Workplace and Worker Safety: Operator safety has always been of paramount importance for any manufacturer. Digital solutions such as image and video Analytics, connected wearables, computer vision, deep learning, robotics and AGVs are widely used to eliminate human errors and make workplaces and shopfloors safer. However, owing to the prevailing COVID-19 crisis, new norms are emerging in workplace and worker safety considerations.
Video analytics based algorithms calculate the physical distance between people and check on protective gear compliance, such as wearing goggles and gloves in the factory. Digital wearables like helmets and global information systems (GIS) are used to geo-fence workers and aid emergency evacuations.
Fig. 4 Representation of manufacturing digital thread
Digital Thread driving Intelligent Production Scheduling and Flexible Manufacturing: Manufacturers are now focusing on flexibility to innovate and be more agile in meeting customer demands.
One of the essential enablers for innovation and agility is a need for the digital thread: a convergence between IT-OT-ET systems ensuring a single source of data thread running through the entire lifecycle of the product across engineering applications, product lifecycle management (PLM), manufacturing execution systems (MES) or manufacturing operations management (MOM) and enterprise applications (ERP) along with quality and lab applications (QMS, LIMS) and field service systems.
An integrated ecosystem ensures constant data integrity and traceability, collaboration across divisions, seamless feedback process and real-time management control towards meeting metrics like on-time delivery, customer schedule adherence and resource idle time.
Remote operations center (ROC): The need for real-time or near real-time decision making has driven organizations to create smart machines and explore the use of IoT technology, including edge processing and edge analytics, to drive fast and informed business and process decisions. There is a need to enable remote decision making and actions in the COVID and post-COVID era. The most widely adopted solution, IoT driven command center dashboards, enables plant operations teams to focus on core production challenges, opportunities, mitigation and augmentation plans based on need. A centralized or a de-centralized remote collaboration center can monitor the plant operations and carry out root cause analysis in case of any failure in the process control layer.
Digital Twin of Assets and Production Process: Enabling effective remote business operations with the least setup time has helped organizations sustain their operations during the lockdown period. The success of digital twins has provided organizations with an impetus to build more such twins to increase operational efficiency in the future. A Digital Twin is, therefore, one of the essential digital solutions for an organization to consider investing in. It involves creating a virtual (digital) representation of a specific manufacturing asset or process across its lifecycle. A digital twin enables a better understanding of what was manufactured, what was designed and how it is operated, bridging the gap between design, implementation and operation. The Digital Twin acts as a single-window for decision making and tracking the performance of an asset or process in their plant through real-time operational data visibility, what-if Simulations and quality control. AR-enabled 3D models help operators do virtual rounds of the shop floor and remote expert support to guide local maintenance staff.
Predictive analytics for asset health and energy consumption: predictability in resource availability and resource consumption are essential for driving efficiencies on the shop floor and ensuring maximum capacity utilization. With limited resources available and high costs incurred during the slowdown period, it has become imperative for organizations to monitor the conditions of assets from the large volumes of data generated by the smart machines and control systems. Based on the failure mode and effect analysis, the anomalies are studied, and diagnostics identified. AI/ML techniques are then used to create prognostic and diagnostic models to predict failures in advance and root cause, impact and resolution identification, transforming asset maintenance from a periodic to a prescriptive activity.
In-process quality Inspection: The quality of products defines the resilience of a manufacturing organization. Hence there is a need for a digital, automated and connected inspection process from design through manufacturing. Digital solutions like vision-based inspections through drones, cobots and robotic inspection, digital twins, image and video analytics ensure consistency of results, quick turnaround, especially in inaccessible areas and for sensitive batch manufactured products.
Augmented digital worker and virtual training: since the breakout of the pandemic, there is an overarching need to reduce human touch and digitize and automate processes to control the spread of the virus. Digital worker solutions address these needs and empower the workforce with actionable, augmented intelligence to improve productivity and quality and enhance safety and avoid compliance risks.
Paperless manufacturing solutions with integrated electronic work instructions, manufacturing process steps with 3D views and AR technologies, autonomous vehicles for transport in factory premises, robotics for quality inspection and automating complex, labor-intensive tasks are examples of digital workers.
Virtualized training environments utilize the knowledge base of past incidents and non-digitized training manuals, AR based models for guiding personnel with augmented instructions for their daily work and fixing machine problems as part of field services. With more customers preferring to stay indoors, there is growing adoption of technology in end user engagement.
Ecosystem visibility: while the digital thread in manufacturing underlines the need for a single thread of data flow across in-house manufacturing systems, Industry 4.0 demands organizations connect their industrial assets, processes, people and systems to the entire manufacturing ecosystem. The current fluctuating demands, frequent rescheduling of delivery schedules and the emergence of new priority items for immediate delivery have created a need for supply chain visibility across the ecosystem for real-time adjustments. A forward and backward supply chain integration between manufacturers, suppliers and logistics providers can be achieved through a connected cloud ecosystem with blockchain ensuring security through its tamper-resistant technology to ensure unscrupulous operators cannot corrupt the data.
A connected cloud ecosystem connectivity ensures visibility to inventory, supply and demand information across partners, enabling agile manufacturing and reducing stockouts or idle inventory.
Multiple wholesale component distributors make delivery commitments based on the OEMs’ inventory picture. They rely on blockchain to trace the lineage of distributed parts across multiple layers of their journey and track sales and procurement prices to settle claims like ship and debit and price protection.
Conclusion
Organizations are often compared to live organisms in their instinct to survive and thrive in challenging environments. The manufacturing world is no different – they need to be resilient and take advantage of the decade’s most significant market disruption. The manufacturers need to innovate their operating model. That is possible only by digitizing their core capabilities. The world is looking at alternative social ways of working in the post-COVID era, which essentially needs greater technology infusion – hence sooner the adoption, faster will be the realization of benefits.
References
- JP Morgan Global Composite PMI https://tradingeconomics.com/world/composite-pmi
- "Pandemic knocks a tenth off incomes of workers around the world." Financial Times. 23 September 2020. Retrieved 23 September 2020.
- Anna-Katrina Shedletsky: The COVID-19 Problems That Will Force Manufacturing To Innovate https://www.forbes.com/sites/annashedletsky/2020/05/05/the-covid-19-problems-that-will-force-manufacturing-to-innovate/#7fab427430d0
- Panel Discussion: Supply Chain Resilience in the New Era: https://www.infosys.com/newsroom/events/2020/supply-chain-resilience.html
- Digital manufacturing in COVID times –Jasmeet Singh, Infosys in conversation with Dominique Raviart, NelsonHall. https://www.infosys.com/industries/industrial-manufacturing/insights/digital-manufacturing-time-covid19.html
Originally published at Infosys - Resilience In Manufacturing Industry
Click through to know more about Enhance Business Value With Digital Engineering Services | Infosys
About the Authors
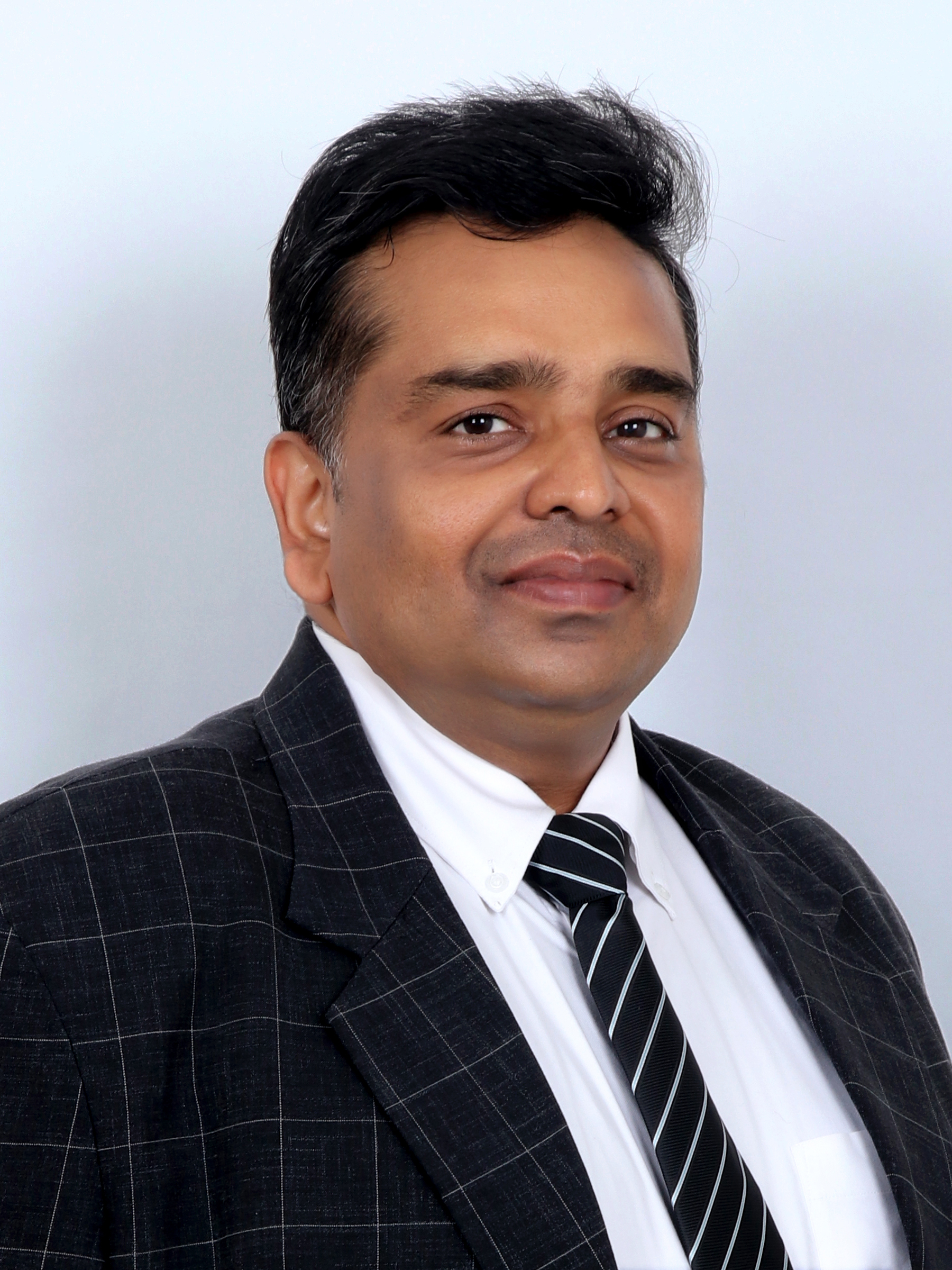
Abhishek Goyal - Vice President and Delivery Head, IoT and Engineering Cloud, Infosys
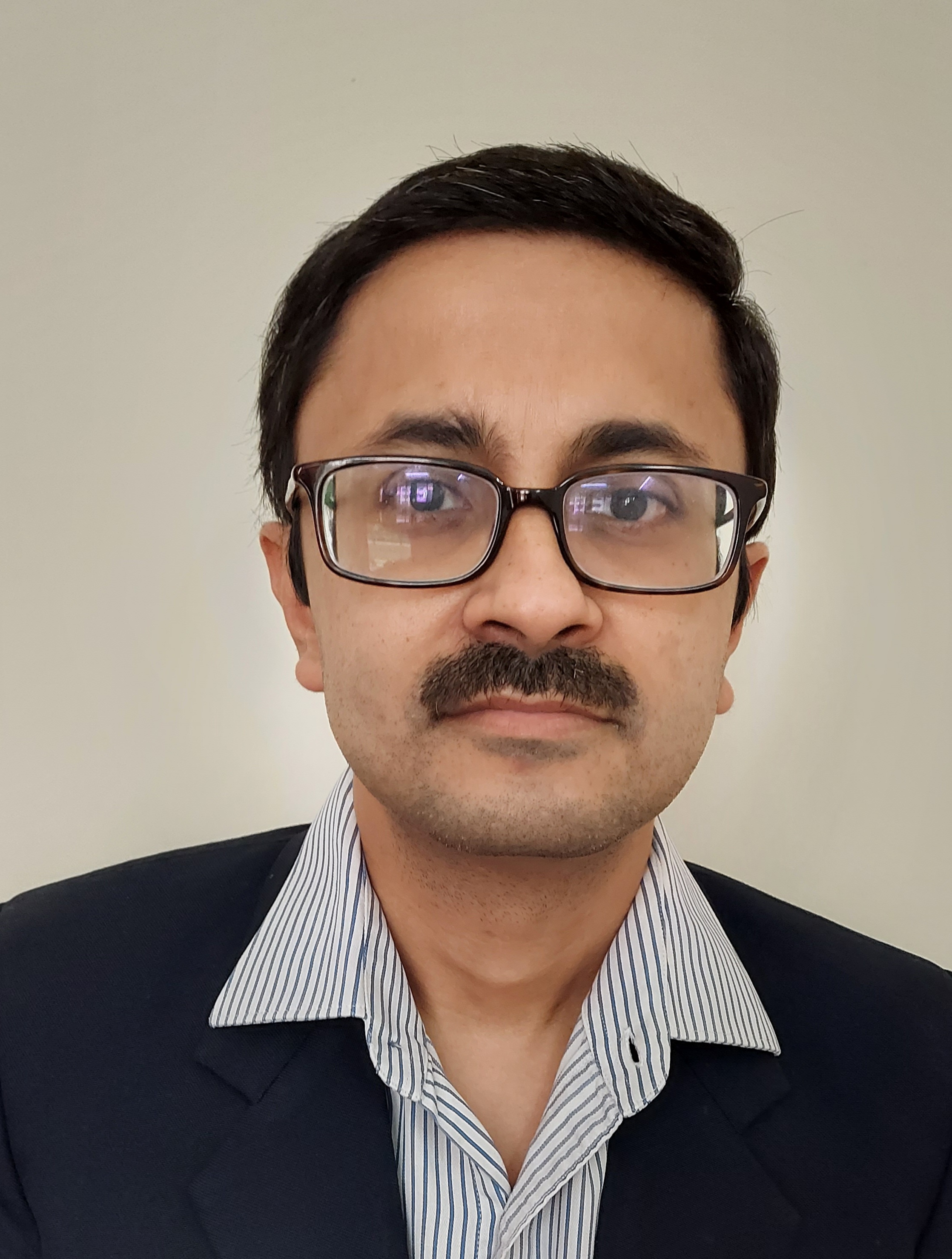
Abhra Dutta - Industry Principal, IoT Center of Excellence, Infosys